Marketing authorisation application checklist for Global Regulatory Affairs Directors
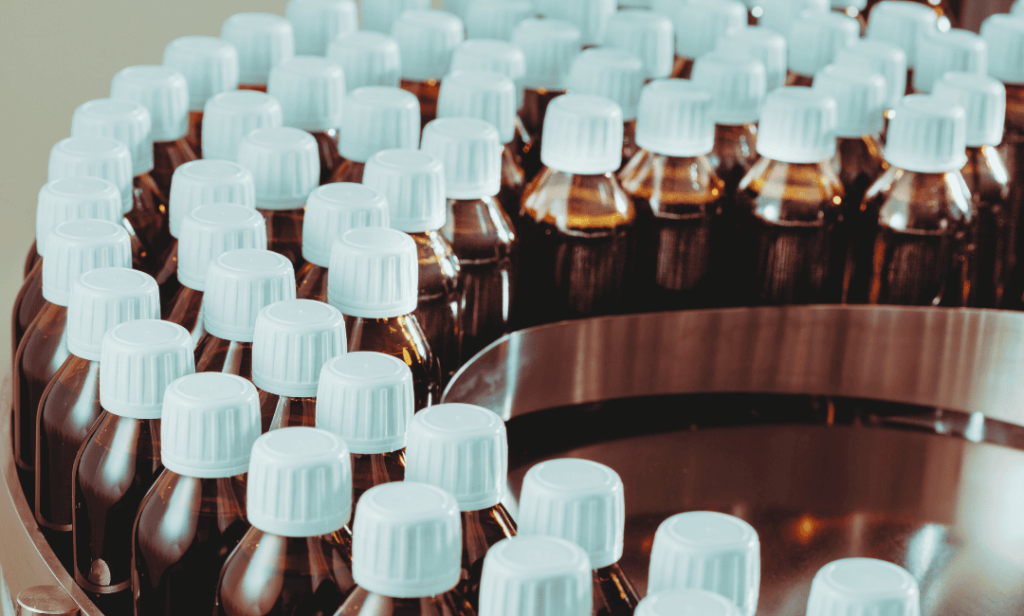
The CMC section of the regulatory dossier stands as one of the cornerstones for achieving a successful global MAA for pharmaceutical products. Regulatory Affairs Directors must often navigate a labyrinth of requirements to ensure compliance across diverse markets, while maintaining the highest standards of product quality.
In this article, we examine the essential factors that should be on every regulatory leader’s radar, including illustrations of common pitfalls and industry challenges.
Related articles:
Keys to managing regulatory affairs in a global MAA project
A guide to labelling in global MAA projects
Regional CMC considerations and preparations
It is essential to grasp the nuances of regional regulatory requirements, particularly the differences in quality expectations among agencies across the world. US and EU requirements may differ from expectations from for instance ASEAN or MENA authorities.
A thorough gap analysis early on of necessary updates to module 3 to comply with specific markets is recommended to understand how much work will be required and how to best fit the current manufacture and supply chain to the local requirements.
To avoid delays in the submission and review processes, especially when seeking simultaneous market approvals across different regions, it is important to understand the critical distinctions between markets. A tailored strategy taking these regional variations into account will enhance readiness and facilitate a smoother registration journey.
Entering rest of the world markets usually means excipients need to comply with market-specific requirements, including approvals for excipients of sensitive origins, for example bovine- or porcine-derived ingredients in regions that necessitate alternatives due to cultural and religious reasons.
This requires manufacturing flexibility, i.e. optimized formulation and manufacturing processes to align with equipment, site capabilities, and regulatory expectations.
Manufacturing Process
Make sure the manufacturing processes in your submission package are thoroughly controlled and validated from active drug substance to final product including all excipients and packaging materials. You want to minimize the risk of exhaustive reviews and requests for clarification, which are both time-consuming and costly. A well-structured manufacturing chain will pave the way for a smoother review process and strengthen confidence in your product’s integrity.
Scale-up considerations can be critical to ensure required capacity and resources. Does the current manufacturing set-up allow for different scales, from pilot batches to possible future batch increases for meeting market demands? Are several manufacturers involved? Are manufacturers in the manufacturing and supply chain compliant with the requirements of the authorities on the markets for which approval is sought? Authorities will request full insight to the complete manufacturing chain, sometimes even demanding on-site inspections.
Stability Studies
Comprehensive stability studies are essential for demonstrating that a pharmaceutical product retains its identity, strength, quality, and purity throughout its designated shelf life.
Failing to provide sufficient long-term stability data for the region in your submission package may compel the regulatory agency to request additional information, inadvertently extending the approval timeline by several months. Early planning and careful execution of preliminary stability studies can serve as a robust strategy for mitigating such risks, ultimately ensuring that the submission is both timely and complete.
Documentation of GMP compliance
Documentation demonstrating compliance with Good Manufacturing Practices (GMP) is essential for successful registration even as regulatory frameworks vary across markets.
Picture a scenario where a global submission encounters rejection due to incomplete GMP documentation. The subsequent financial ramifications and project delays can be substantial. By implementing rigorous documentation practices and promoting a culture of compliance within the organization, you can significantly reduce the likelihood of such setbacks.
Implementing Quality by Design (QbD) principles align with the stringent expectations set forth by agencies such as the FDA and EMA and since many worldwide authorities rely on approvals by FDA and EMA, a QbD strategy can ease regulatory burden.
Risk management and lifecycle approach
Use a risk-based approach to evaluate the CMC components, focusing on how changes in raw materials, processes, or specifications could affect product quality.
Develop a lifecycle management plan to track and manage potential changes in manufacturing or supply, ensuring continuous improvement and staying compliant with regulations throughout the lifetime of the product.
Conclusion
The journey through the CMC dimensions of a global MAA project is undoubtedly complex, loaded with potential pitfalls that can compromise timelines and resources. By gaining a comprehensive understanding of the key factors and anticipating common challenges, Regulatory Affairs Directors can position their organisations for success.
Collaborating with regulatory consultants who specialize in CMC not only provides invaluable expertise and flexibility but also serves as a strategic advantage that can save both time and money. As the landscape of global regulatory affairs continues to evolve, a proactive approach to CMC planning will facilitate smoother approval processes and reinforce the quality and reliability of your pharmaceutical products.
The Arex Regulatory Affairs team has the skills and experience to complete your team in global MAA projects.
Read more about valuable services for global projects:
Regulatory Affairs
CMC